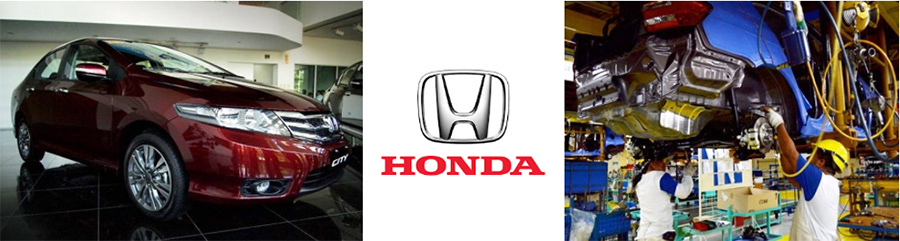
For over two decades, Honda Cars Philippines’ facility in Santa Rosa, Laguna, has been manufacturing affordable and high-quality automobiles. From the legendary EG Civic to the newest GM City, all units produced at this plant have been assembled with the greatest of care. I’ve always felt that the Philippine-made cars have had an edge over other Hondas made outside Japan. Maybe it’s that extra attention to detail that our countrymen put into their work, but it has always been a point of pride for me, despite not being a flag-waving cheerleader for the “Proudly Philippine-made” set.
Recently, we were invited to tour the facility to see for ourselves what went into making the Honda City, in particular, the new EL and ENC variants. The HCPI facility has the capacity to build 15,000 City sedans a year, with a separate sub-assembly line ready for other products. While it doesn’t run at full capacity, they have so far produced over 70,000 City units since 1996. And production has been steadily growing with the introduction of the new “GM” generation.
Currently, production runs at about 30 cars a day with a single shift. The shells glide around hanging from overhead conveyors, clothed in rubber fender protectors to prevent damage to the bodywork. While panels are imported from Thailand, the body shell, the crash structure and the sub-assemblies are all put together and welded on-site. Workers then meticulously check the straightness of the body and smoothness of the panels before the comprehensive five-dip corrosion treatment and painting. Rusting fenders on Hondas? A thing of the past. Engines and transmissions are also assembled on-site. If you believe girls don’t know how to wrench, the piston assemblies on your City would like to disagree with you. After assembly, engines are tested for defects before going out to the final assembly line.
It’s here that everything comes together. Everything from the revolutionary mid-chassis fuel tanks to the equally revolutionary ULT seats are stacked in bins waiting to go into the car. After every panel is fitted, every wire is tucked and every bolt is tightened, the cars go on to quality checking.
If you’re the kind who believes in turtle-slow break-ins, you’re in for a shock. Even before the car has left the factory grounds, it has been revved to kingdom come, the brakes slammed, the door seals blasted with 20psi of water, and the suspension subjected to a zip around a track best described as “farm-road level.” All of these are done in the name of quality control.
Notice: Images and logos is for illustration purposes only and not intended for patent infringement